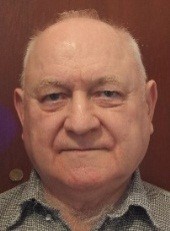
Seongwoo Woo
Faculty of Mech. Engineering
Title: Reliability Design Of Mechanical Systems Such Subjected To Repetitive Stresses
Biography:
Dr. Woo has a BS and MS in Mechanical Engineering, and he has obtained PhD in Mechanical Engineering from Texas A&M. He major in energy system such as HVAC and its heat transfer, optimal design and control of refrigerator, reliability design of mechanical components, and failure Analysis of thermal components in marketplace using the non-destructive such as SEM & XRAY. Especially, he developed parametric accelerated life testing (ALT) as new reliability methodology. If there is design fault in the mechanical system that is subjected to repetitive stress, it will fail in its lifetime. Engineer should find the design faults by parametric ALT before product launches. In 1992–1997 he worked in Agency for Defense Development, Chinhae, South Korea, where he has researcher in charge of Development of Naval weapon System. In 2000-2010 he had been working as a Senior Reliability Engineer in Side-by-Side Refrigerator Division, Digital Appliance, SAMSUNG Electronics, where he focused on enhancing the life of refrigerator as using parametric the accelerating life testing. Now he is working as associate professor in mechanical department, Addis Ababa Science & Technology University.
Abstract
The basic reliability concepts - parametric ALT plan, failure mechanism and design, acceleration factor, and sample size equation were used in the development of a parametric accelerated life testing method to assess the reliability quantitative test specifications (RQ) of mechanical systems subjected to repetitive stresses. To calculate the acceleration factor of the mechanical system, a generalized life-stress failure model with a new effort concept was derived and recommended. The new sample size equation with the acceleration factor also enabled the parametric ALT to quickly evaluate the expected lifetime. This new parametric ALT should help an engineer uncover the design parameters affecting reliability during the design process of the mechanical system. Consequently, it should help companies improve product reliability and avoid recalls due to the product failures in the field. As the improper design parameters in the design phase are experimentally identified by this new reliability design method, the mechanical system should improve in reliability as measured by the increase in lifetime, LB, and the reduction in failure rate,ï¬ As a test case, two cases were studied: 1) failed reciprocating compressors of French-door refrigerators returned from the field and 2) the redesign of hinge kit system (HKS) in a refrigerator. After a tailored of parametric accelerated life testing, the mechanical systems such as compressor and hinge kit system (HKS) with corrective action plans were expected to achieve the lifetime target – B1 life 10 years.
- Emerging Smart Materials
- Materials and Science Engineering
- Carbon Nanotubes, Graphene and Composites
- Material Synthesis and Characterization
- Nanotechnology
- Piezoelectric Materials and 3-D Printing
- Materials Engineering
- Polymer Science and Engineering